What is SAP Production Planning?
SAP Production Planning (SAP PP) is the component of ERP Central Component (SAP ECC) that helps businesses plan the manufacturing, sale and distribution of goods. It plays a vital role in a manufacturer's supply chain by providing numerous functionalities for production planning, execution and control.
Production planning and execution are important activities in any manufacturing operation, however, these activities can be complex. SAP PP helps manufacturing businesses to optimize and manage their production processes and meet their goals.
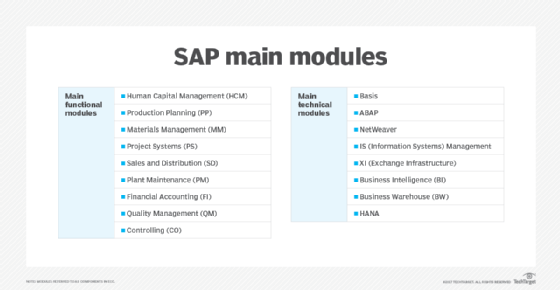
Key features in SAP Production Planning
Various features and functionalities in SAP PP help manufacturers to streamline their production processes, including the following:
- Demand planning and forecasting.
- Capacity planning.
- Material requirements planning (MRP).
- Sales and operations (S&O) planning.
- Production orders (creation and management).
- Shop floor control.
Reporting and analytics tools enable manufacturing organizations to monitor key performance indicators (KPIs) related to production planning and control. They can also track production costs and analyze production variances, then implement the insights from these analyses to improve decision-making.
Material requirements planning
SAP PP provides information about current inventory levels, production schedules and lead times. This data can be used to optimize inventory management and scheduling, and to manage production activities to ensure timely production.
Demand planning
SAP PP analyzes large quantities of historical data using advanced statistical models. It then generates forecasts about future demand, which helps managers and decision-makers execute plans to meet demand. For example, they can take steps to optimize inventory levels and avoid stockouts (or wastage).
Capacity planning
Manufacturers can analyze their current production capacity and assess if it can be improved without significantly adding resources or overburdening existing resources. By optimizing resource utilization, they can improve production efficiency, balance workloads and remove undesirable production bottlenecks that may lead to delays or complaints.
Production planning
SAP PP can hold the exact instructions, procedures and timelines for manufacturing a particular product. This enables workers to produce the product exactly as per specifications. It also helps the manufacturing organization to minimize errors or defects and maintain product quality and consistency. Also, SAP PP tracks the progress of each order, allowing managers to implement quick and early adjustments to ensure that the final product matches the given specifications.
Benefits of SAP Production Planning
By providing updated, real-time information about many aspects of production, managers and other personnel can streamline manufacturing processes like capacity planning, MRP, production order confirmation, inventory management and demand forecasting. They can also make quick adjustments to production plans if demand or capacity changes or if there are supply chain disruptions to maintain production timelines.
Production managers can also find areas of improvement and implement measures to eliminate them. For example, they can find instances of material non-availability or equipment downtime. Or they can discover that the production schedule is lagging behind the demand, or that there's a mismatch between available capacity and required capacity to meet a production target.
SAP PP also supports optimizing inventory management. Managers can implement MRP and demand planning processes to minimize inventory stockouts, eliminate wastage and optimize costs. This helps to ensure that production continues uninterrupted, minimize the potential for customer complaints and improve customer satisfaction.
Since decision-makers get deep insights and visibility into the end-to-end production cycle, they can make more informed decisions to benefit the organization and its customers.
Finally, SAP PP can support the manufacturing organization's quality goals. It can set high-quality targets and meet them by tapping into data, reports and insights. This ensures that only high-quality products reach the market.
Integration with other SAP modules
SAP PP seamlessly integrates with other ECC components, including Materials Management, Sales and Distribution, Plant Maintenance, Quality Management, Finance and Controlling, and Human Capital Management. This integration provides visibility into the entire production lifecycle.
Such visibility is crucial to control the lifecycle and minimize any undesirable variances. It also enables manufacturers to implement a more holistic approach to manage and optimize various production activities and achieve desirable outcomes.
Master data in SAP PP
Everything in SAP PP revolves around master data that is stored and manipulated in centralized master data tables. There are five types of master data that are maintained in SAP PP:
- Material master. Containing information on the materials procured, produced, stored or sold by the organization, it is used to plan materials requirements, guide purchase decisions, update goods issue or receipts in inventory management, verify invoices, fulfill sales orders and confirm production.
- Work center. Contains information about production machines (or groups of machines), specifically, data about capacity, scheduling and costing.
- Bill of materials. BOM is a structured list of the names and quantities of various components needed to produce or assemble the organization's product; it is used for material requirements planning and product costing.
- Routing. Lists the sequence of operations performed at the work center and the time taken to execute those operations.
- Production version. Links the BOM and routing data to support production processes.
In SAP PP, all production master data is created at the plant level. Planning activities are also performed at the plant level. However, the production confirmation process can happen at the plant or storage site level. Once the confirmation is available, goods movement also happens at the plant or storage site level. These aspects refer to the organizational structure in the live SAP PP module.
Who can use SAP Production Planning?
SAP PP can be configured to meet various industry requirements and includes a number of modules that support specific manufacturing industry types, including discrete manufacturing, repetitive manufacturing and process manufacturing.
In discrete manufacturing, the numbers of goods produced change by lot, and costs are calculated by orders and lots. In repetitive manufacturing, products remain unchanged over long periods of time and production occurs in total quantities, not individual lots.
In process manufacturing, products are manufactured in batch-sized lots using a process described in a master recipe that can be adjusted for individual batches. Process manufacturing is used primarily in the chemical, pharmaceutical, and food and beverage industries.
SAP Production Planning in S/4HANA
S/4HANA is SAP's ERP solution based on the SAP HANA in-memory database. The ERP provides intelligent automation features to streamline business processes, and incorporates many advanced technologies like AI, machine learning and analytics to support business decision-making.
SAP PP in S/4HANA includes more features and capabilities for production planning and optimization. For example, it provides a functionality called monitor material coverage which enables production managers to check materials coverage and address shortages. This feature is not supported in ECC (6.0). Other SAP PP functionalities available in S/4HANA but not in ECC include the following:
- Manage material coverage.
- Monitor external requirements (from sales orders).
- Manage external requirements.
- Monitor internal requirements.
- Manage internal requirements.
- Manage change requests.
See how to think long term about SAP ECC customizations and check out steps for creating an analytics strategy on SAP ECC.